>
Sputtered Solar Absorbing Coatings
1. Solar
selective absorbing coatings
All bodies emit
thermal radiation. An ideal solar selective surface absorbs most
of incident solar radiation while simultaneously suppressing emittance
itself. Commonly quoted parameters of performance are solar absorptance
and thermal emittance. Most solar selective coatings use metal-dielectric
composites, known as cermets, as the absorber of solar energy. Electroplated
black chromium is most popular solar selective absorber. Nicked-pigmented
anodic Al2O3 solar absorber is another popular solar selective absorber.
The costs of the production of these two kinds of solar coatings
are low, so they are widely used in flat plate solar collectors
for solar hot water application. However the emittance of both coatings
is high, around 0.1 - 0.2 at 100°C.
2. Graded
SS-C cermet solar coatings
Magnetron sputtering
technology has also been used for the deposition of solar selective
absorbing coatings with improved solar performance, in particular,
lower emittance and less environmental pollution than electrochemical
methods. The School of Physics within the University of Sydney have
achieved several innovations of solar selective coatings in the
last two decades. Selective surfaces, incorporating DC reactively
sputtered stainless steel-carbon (SS-C), were intensively studied
in this school during 1970s to 1980s. The all-glass evacuated solar
collector tubes, incorporating DC reactively sputtered graded SS-C
cermet selective coatings, have been mass-produced in Japan. A solar
absorptance of 0.88-0.92 and emittance of 0.05 - 0.07 at 80°C
have been archived for mass-produced SS-C cermet solar collector
tubes.
3. Graded
Al-N cermet solar coatings
Reactive sputtered
Al-N cermet solar coating was initiated in this school in 1980s.
The all-glass evacuated solar collector tubes, incorporating DC
reactively sputtered graded Al-N cermet selective coatings, have
been mass-produced in China in large capacities, more than 10 million
tubes a year in 1999. A solar absorptance of 0.88-0.92 and emittance
of 0.06 - 0.10 at 80°C have been archived for mass-produced
SS-C cermet solar collector tubes.
Cylindrical DC magnetron sputter coater has been used to manufacture
economically the SS-C and Al-N cermet solar collector tubes.
4. Graded
Mo-Al2O3 cermet solar coatings
Graded Mo-Al2O3
cermet solar collector tubes that were manufactured by Luz Co. Israel,
were used for solar thermal power plants constructed in Southern
California during 1984 -1990. Nine plants with a total net electricity
capacity of 354 MW are under operation to feed electricity in the
grid of the regional utility. Mo-Al2O3 cermet solar coatings were
deposited by using conventional magnetron sputtering technology.
The Mo metal component in the cermet is deposited using DC sputtering
and the ceramic component is deposited by RF sputtering. A solar
absorptance of 0.96 and emittance of 0.16 at 350°C were archived.
5. Double
cermet layer solar coatings - Achieving the highest solar performance
Recently we
have made two very significant innovations related to solar selective
coatings, double cermet layer structure for achieving the highest
solar performance and metal-aluminium nitride (M-AlN) solar selective
coatings deposited by a novel two-target DC magnetron sputtering
technology for reducing the costs of high-temperature solar coatings.
Through fundamental analysis and computer modelling, we have developed
a double cermet film structure for solar selective surfaces and
achieved theoretically and experimentally better solar performance
than surfaces using a homogeneous cermet layer or the conventional
graded film structure. In the double cermet layer solar coatings,
solar radiation is effectively absorbed internally and by phase
interference. This innovation has been patented in Australia, USA
and other several countries. A typical double cermet film structure,
as schematically shown in Fig. 1, from substrate to surface consists
of:
- a metal infrared
reflecting layer;
- an absorbing
layer composed of two homogeneous cermet sub-layers, the layer
near the metal infrared layer has a high metal volume fraction
(HMVF) and the layer near the anti-reflection layer has low metal
volume fraction (LMVF); and
- an anti-reflection
layer composed of a transparent dielectric material.
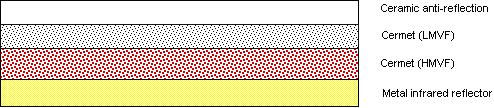
Fig.1.
Schematic diagram of a solar selective absorber with double cermet
layers, a low metal volume fraction (LMVF) cermet layer on a high
metal volume fraction (HMVF) layer on a metal infrared reflector
with a ceramic anti-reflection layer.
We have developed
a computer modelling for design of solar selective coatings. As
an example, a predicted normal reflectance spectrum of a Mo-Al2O3
cermet selective surface is shows in Fig. 2. The reflectance spectrum
corresponds to a solar absorptance of 0.965 and normal emittance
of 0.031 at 20°C. A near normal reflectance spectrum of a deposited
film (dot points) is also shown in Fig. 2. This reflectance spectrum
corresponds to a solar absorptance of 0.96, and near normal emittance
of 0.03 at room temperature. Both calculated and deposited films
have the same film structure, Al2O3/Mo-Al2O3(LMVF)/Mo-Al2O3(HMVF)/Cu.
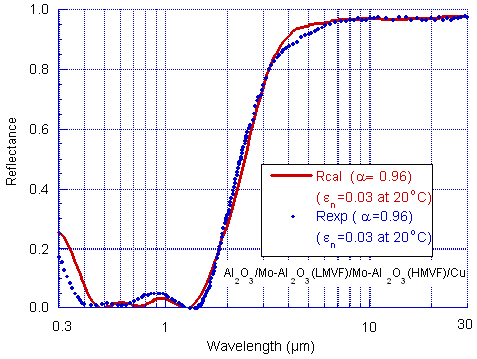
Fig.2.
Two normal reflectance spectra for a calculated (solid line) and
a deposited (o o o points) Mo-Al2O3 cermet solar coating. Both films
have the same film structure: Al2O3/Mo-Al2O3(LMVF)/Mo-Al2O3(HMVF)/Cu.
6. M-AlN
cermet solar coatings by a novel two-target DC sputtering - Reducing
the costs of high-temperature solar coatings
We have invented
a series of new cermet materials for solar selective coatings deposited
by a novel two-target DC magnetron sputtering technology. The ceramic
and metallic components in the cermet are simultaneously deposited
by DC sputtering, running two metallic targets. Ceramic component
is deposited by DC reactive sputtering and metallic component by
DC non-reactive sputtering. A patent application describing these
new solar selective coatings has been lodged.
A series of
metal-aluminium nitride (M-AlN) cermet solar coatings have been
deposited using a planar magnetron sputter apparatus at the laboratory.
An Al metal target is used to deposit AlN ceramic component in the
cermet by DC reactive sputtering in a gas mixture of argon and nitrogen.
Other metallic targets, including SS, W, Ni80Cr20 and Mo based alloy
TZM, which have good nitriding resistance, are used to deposit the
metallic component in the cermet by DC non-reactive sputtering in
the same gas mixture. The solar absorptance of 0.94 - 0.96, and
normal emittance of 0.03 - 0.05 at room temperature has been achieved
for the deposited M-AlN cermet selective coatings with the double
cermet layer structure.
7. Mass-produced
double Al-N cermet layer solar collector tubes
We have made
very successful commercial development of above two new innovations
in collaboration with Peking University and Himin Solar Energy Company,
China.
Figure 3 (a
photograph) shows two cylindrical DC magnetron sputter coaters,
installed at a production line in China, for depositing Al-N cermet
solar coatings onto batches of tubes. A cross-section schematic
of the vacuum chamber is shown in Fig. 4.
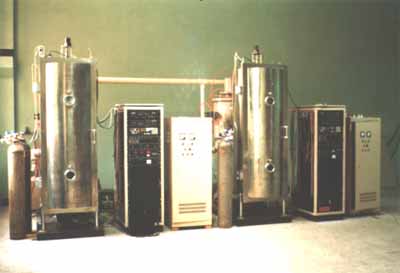
Fig.3.
Photograph of two commercial-scale cylindrical DC magnetron sputter
coaters, installed in a production line, for depositing Al-N cermet
solar coatings onto batches of tubes. The vacuum chamber, 1.9 m
high, is on the left. The front door of the chamber is for manual
loading of tubes. A DC power supply unit (40A/600V) for sputtering
is shown on the right. The control cabinet is in the middle between
the chamber and the DC power unit.
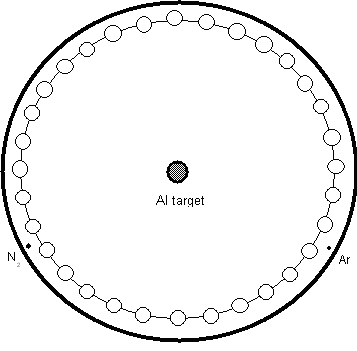
Fig. 4.
A cross-sectional schematic view of a cylindrical DC magnetron sputter
coater for depositing Al-N cermet selective surfaces onto batches
of tubes. A cylindrical aluminium target is set at the centre of
the chamber. Thirty-two glass tubes of outside diameter 37 mm and
length 1.5 m may be accommodated in the vacuum chamber.
Borosilicate
glass tubes are used in mass-production. During sputter coating
the glass tubes are given planetary rotation to ensure coating uniformity.
Al-N cermet solar selective coatings with double cermet layer film
structure, AlN/Al-N(LMVF)/Al-N(HMVF)/Al/Al-N(adhesion) are deposited
onto batches of tubes using the sputter coater. A solar absorptance
of 0.95 - 0.96 and a thermal emittance of 0.06 - 0.09 at room temperature
have been achieved.
8. Mass-produced
double SS-AlN cermet layer solar collector tubes
Commercial-scale
cylindrical DC magnetron sputter coater has been developed for deposition
of SS-AlN solar selective coatings onto batches of tubes, one installed
at Peking University, another installed at the University of Sydney.
A cross-section schematic of the vacuum chamber is shown in Fig.
5. A solar absorptance of 0.95 - 0.96, and emittance of 0.05 - 0.08
at 80°C has been achieved for the SS-AlN cermet selective surface
coatings with the Al or Cu metal infrared reflector layer. The absorptance
variation along the length of tubes is less than 1%. Figure 6 shows
the reflectance spectrum of a deposited solar selective surface
with double SS-AlN cermet layers. This film has the solar absorptance
of 0.95 and emittance of 0.05 at 20°C. These SS-AlN cermet solar
collector tubes are stable at 300 - 350°C.
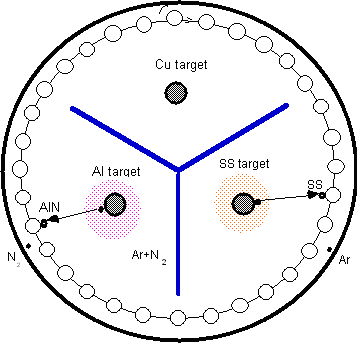
Fig.5.
A cross-sectional schematic view of a cylindrical DC magnetron sputter
coater for depositing M-AlN cermet selective surfaces onto batches
of tubes. Three cylindrical cathodes consist of Al, SS and Cu tubes,
are separated by a screen to prevent cross contamination. Thirty-two
glass tubes of outside diameter 37 mm and length 1.5 m may be accommodated
in the vacuum chamber. Two DC power units (50A/600V each) are for
depositing SS-AlN cermet layer.
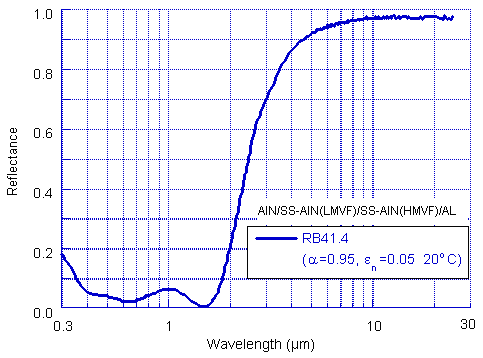
Fig.6.
The reflectance spectrum of SS-AlN cermet solar selective coating
deposited using a commercial-scale DC sputter coater. The corresponding
film has a double cermet film structure AlN/SS-AlN(LMVF)/SS-AlN(HMVF)/Al
and a solar absorptance of 0.95 and normal emittance of 0.05 at
20°C.
Himin Solar
Energy Company, China has mass-produced advanced Al-N and SS-AlN
cermet solar collector tubes under a licence agreement with the
University of Sydney. Currently Himin Solar Energy Company has manufactured
three different series of advanced solar collector tubes, TS-AA,
TS-SA and TS-SC. Enquiries for more information about solar collector
tubes should be directed to
Himin Solar
Energy Company, China
Website: http://www.himin.com/english/index.htm
(functions best using Internet Explorer)
9. Double
W-AlN and Mo-AlN cermet layer solar collector tubes
Using above
commercial-scale coater, it would be possible to produce high-temperature
W-AlN and Mo-AlN cermet solar collector tubes. The procedure for
deposition of the W-AlN and Mo-AlN cermet solar coatings is similar
to that for SS-AlN cermet coatings. In order to improve further
the thermal stability of the solar coatings at high temperature,
It is also possible to deposit a metallic W or Mo layer as the infrared
reflector. The W-AlN and Mo-AlN cermet solar coatings are being
commercially developed.
The costs of
the M-AlN cermet solar coatings are expected to be slightly higher
than the Al-N cermet solar coatings. These M-AlN cermet solar collector
tubes have the potential for widespread applications, in particular,
for solar thermal electricity. The availability of these low-cost
high-temperature M-AlN cermet solar collector tubes will open up
the possibility for the design of a high-temperature solar collector
system for solar thermal electricity generation at low cost than
previously contemplated. Recently a Compact Linear Fresnel Reflector
(CLFR) configuration has been proposed for solar thermal power plant.
Flat mirror strips direct solar radiation to both sides of a rack
of vertically oriented evacuated tubes.
[1] Very Low
Emittance Solar Selective Surfaces Using New Film Structure. Q.-C
Zhang and D. R. Mills, J. Appl. Phys. 72, 3013-3021(1992).
[2] High Efficiency Mo-Al2O3 Cermet Selective Surfaces for High-temperature
Application. Q.-C Zhang, Y. Yin and D. R. Mills, Sol. Energy Mater.
Sol. Cells 40, 43- 53(1996).
[3] Direct Current Magnetron Sputtered W-AlN Cermet Selective Surfaces.
Q.-C. Zhang, J. Vac. Sci. Technol. A vol.15, pp.2842-2846(1997).
[4] Metal-AlN Cermet Selective Surfaces Deposited by Direct Current
Magnetron Sputtering Technology. Q.-C. Zhang, J. Physics D: Appl.
Phys. 31, 355-362(1988).
[5] A Cylindrical Magnetron Sputtering System for Depositing Metal-AlN
Cermet Solar Coatings onto Batches of Tubes. Q.-C. Zhang, K. Zhao,
B.-C. Zhang, L.-F. Wang, Z.-L. Shen, Z.-J. Zhou, D.-Q. Lu, D.-L
Xie and B.-F. Li, J. Vac. Sci. Technol. A16, 628-632 (1998).
[6] High Performance Al-N Cermet Solar Coatings Deposited by a Cylindrical
DC Magnetron
Sputter Coater. Q.-C. Zhang, K. Zhao, B.-C. Zhang, L.-F. Wang, Z.-L.
Shen, Z.-J. Zhou, D.-Q. Lu, D.-L Xie and B.-F. Li, Vac. Sci. Technol.
A17, 2885-2890 (1999).
Enquiries
Enquiries for
more information should be directed to:
Dr. Qi-Chu Zhang
School of Physics, A28
The University of Sydney
NSW 2006, Australia
Phone: +61-2-9351 318
Email: zhang@physics.usyd.edu.au
|